The centaur Nessus, a hybrid of man and horse, was commissioned by Hercules to help his wife Deïaneira cross a river. Overcome by lust, he suddenly wanted to kidnap the beautiful woman, whereupon the enraged Hercules killed him with an arrow. This virtuosically modelled, subtly erotic group came to Dresden as a diplomatic gift in 1587 together with three other small bronzes by the Medicean court sculptor and is one of the most beautiful casts of this popular model.
Further Media
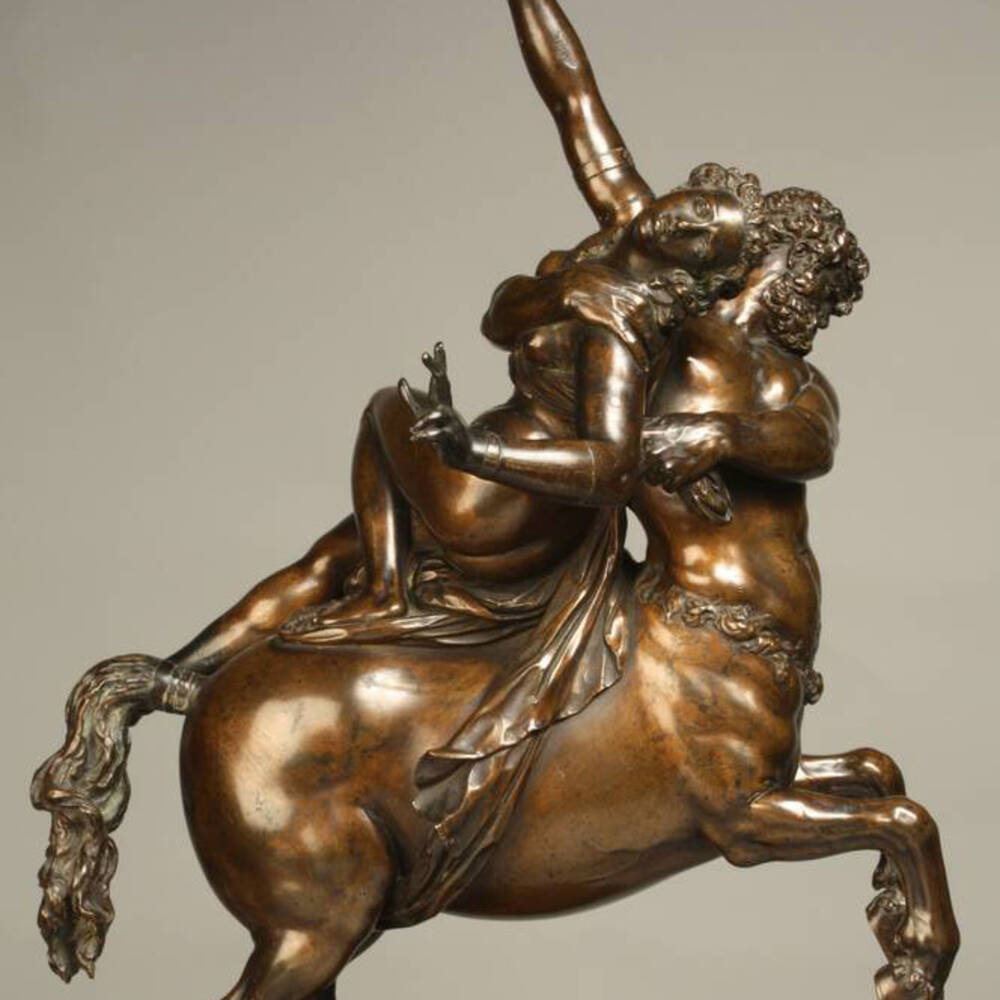
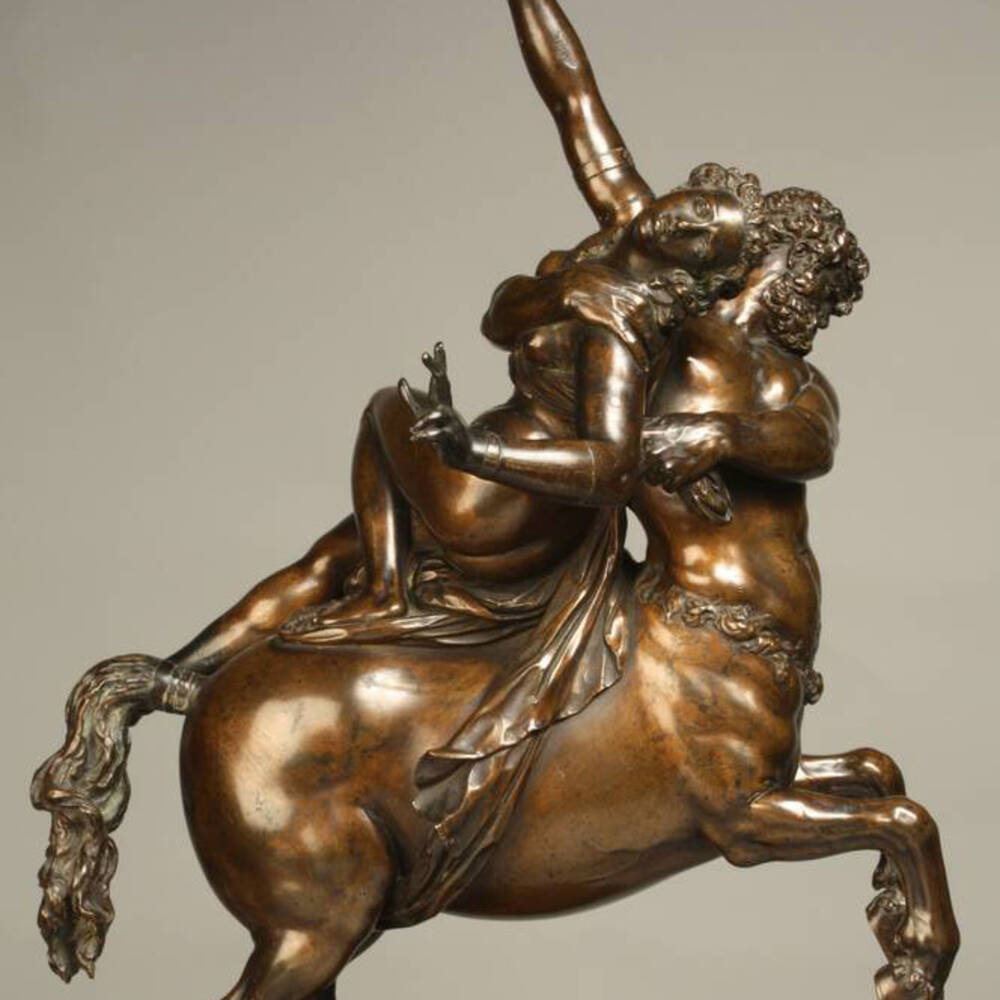
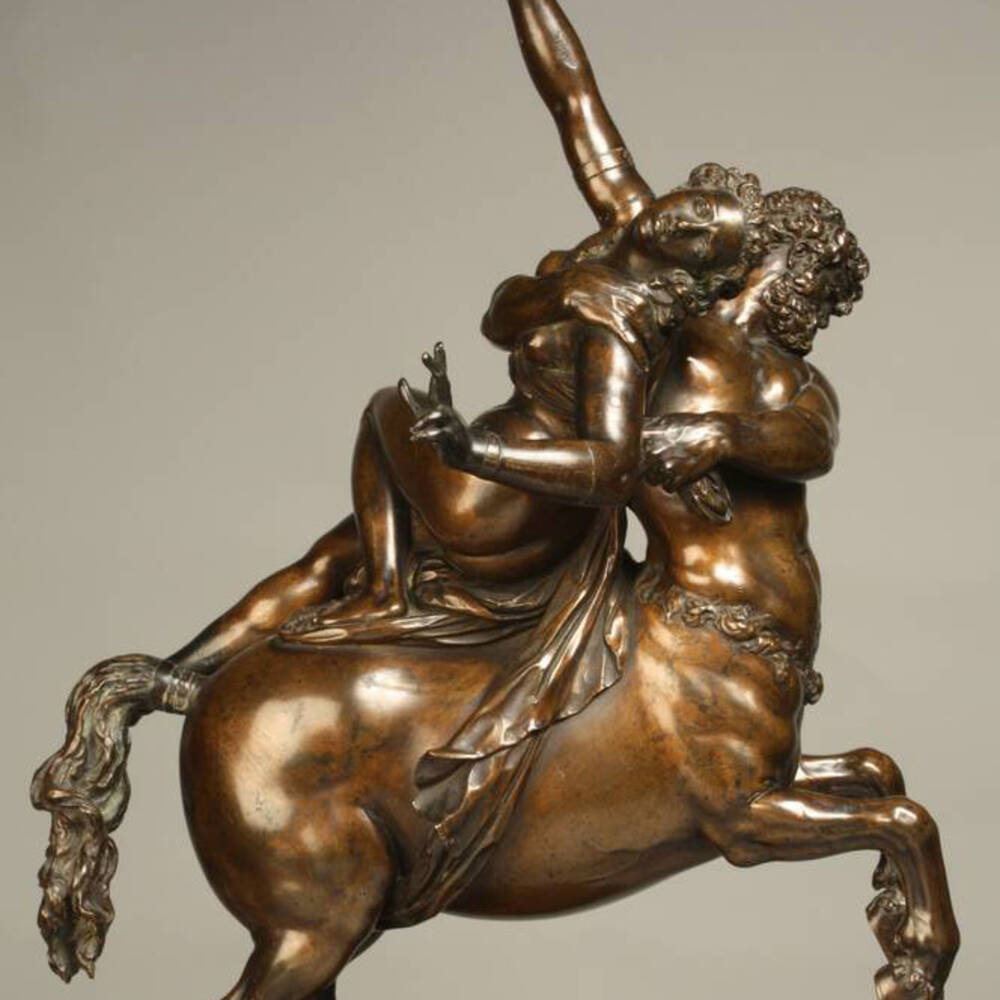
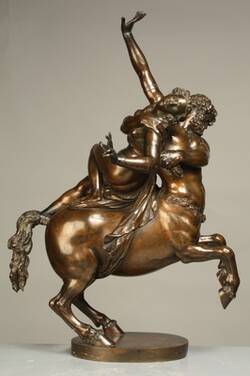
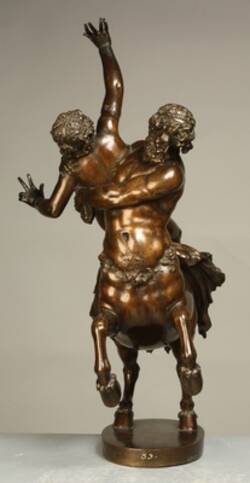
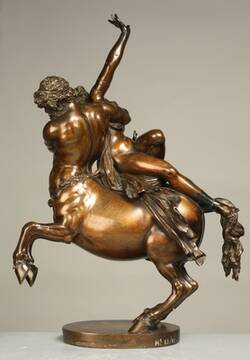
This bronze statuette is inspired by a scene in the Metamorphoses by the Roman poet Ovid. In his collection of lyrical tales, Ovid recounts the story of the beautiful princess Deianira, who married Hercules. On their way to Thebes, they came to a river turned into a torrent by floods. The centaur Nessus lived near the river and offered them his help. First he carried Hercules across to the other bank. But when Nessus returned and Deianira climbed onto his back, he was overcome by his passion for her and decided to abduct her. As Nessus galloped off with her, Hercules placed a poisoned arrow into his bow, fired and hit the centaur.
Mortally wounded, Nessus decided to have his revenge and told Deianira to collect some of his blood. If she poured it onto her husband’s tunic, he said, it would ensure his eternal love.
Much later, in a moment of jealousy, Deianira remembered Nessus’s words and smeared the blood onto her husband’s lionskin shirt. But since the blood also contained the poison from the arrow, Hercules suffered terrible agonies. As the shirt burned and ate into his body, it was impossible to take it off. Deianira, realising what she had done, was plunged into despair and killed herself. The pain Hercules endured was so intense that he saw no other way out than to end his own life, and he threw himself onto the funeral pyre. Here, then, Giambologna has captured in bronze the fateful turning point in the story.
Giambologna’s works were highly coveted by Europe’s noble dynasties. The demand was so great, he was soon unable to satisfy it working alone. So he started producing his small bronze statuettes with the help of a well-organised workshop. This allowed him to use the sophisticated technique of bronze casting to make a number of copies of each ‘autograph’ wax model – that is, one made by his own hand. He left the creation of the mould and casting to his assistants. Then under Giambologna’s supervision, the cast from the mould was cleaned and chased by goldsmiths.
But when more reproductions are taken from one wax model mould, the less precise the details on the cast become. And that means more processing afterwards – or cold working, as it is known.
If you take a moment to look at this bronze, you’ll realise this must be one of the very early casts of the Nessus and Deianira statuette. All the details are clearly visible – the centaur’s thick, matted hair, Deianira’s hair, the material of the cloth, and the fine blood vessels on the horse’s body.
The shimmering surface of the figures is a result of a mixture of resins and oils burned into the statuette. The composition of this mixture was a secret only known to Giambologna’s workshop – a secret no one has yet succeeded in unlocking.
The technique of bronze casting is over 2000 years old. The process, which is quite complex, begins with the artist modelling a figure from wax. The wax figure is then coated with clay and allowed to dry. When the mould is heated, the outer layers of clay are baked and the soft wax inside melts leaving the mould to cast the bronze.
However, given the risk of damage when removing an entire mould, a figure is often not cast as one unit, but in individual pieces. In the next stage, enough molten wax is poured into the moulds to form an even wax layer inside. This needs to be as smooth as possible since it later corresponds exactly to the figure’s ‘bronze skin’. The rest of the hollow mould is then filled with a mix of wet clay and sand. When this core has hardened, the individual pieces covered in wax can be removed from their moulds and joined together to form the entire figure. The pieces are joined with core pins and the wax edges smoothed and joined with a hot knife. At this point, the wax intermodel, as it is called, is fully assembled. In the next stage, wax rods are added to the intermodel to provide channels for the bronze during the casting process.
Then the outer mould is built up. To ensure every detail is reproduced, the clay coating over the figure is added layer for layer. After it has been fired, the massive form is inverted so the melted wax can flow out. As the wax rods, known as sprues, melt and form hollow channels, they provide the route to pour in the hot molten bronze into the mould, and at the same time let the air escape. After the metal cools, the sprues are sawn or chiselled off, the holes filled and, in the last step, the surface cleaned, smoothed and polished.
- Location & Dating
- before 1587
- Material & Technique
- Bronze
- Dimenions
- H: 42,4 cm, B: 29,2 cm, T: 21,2 cm
- Museum
- Skulpturensammlung
- Inventory number
- H2 023 / 095