The statuette is a scaled-down and free replica of the ancient equestrian statue of Marcus Aurelius in Rome. Thanks to the unusual inscription on the base plate, it is known that Filarete created it while working on the bronze doors for St. Peter's Basilica. It is considered the first small bronze of the Renaissance and the founding work of this genre inspired by antiquity, which, unlike sculpture before it, serves no purpose (e.g. for religious devotion) but only the pleasure of the collector.
Further Media
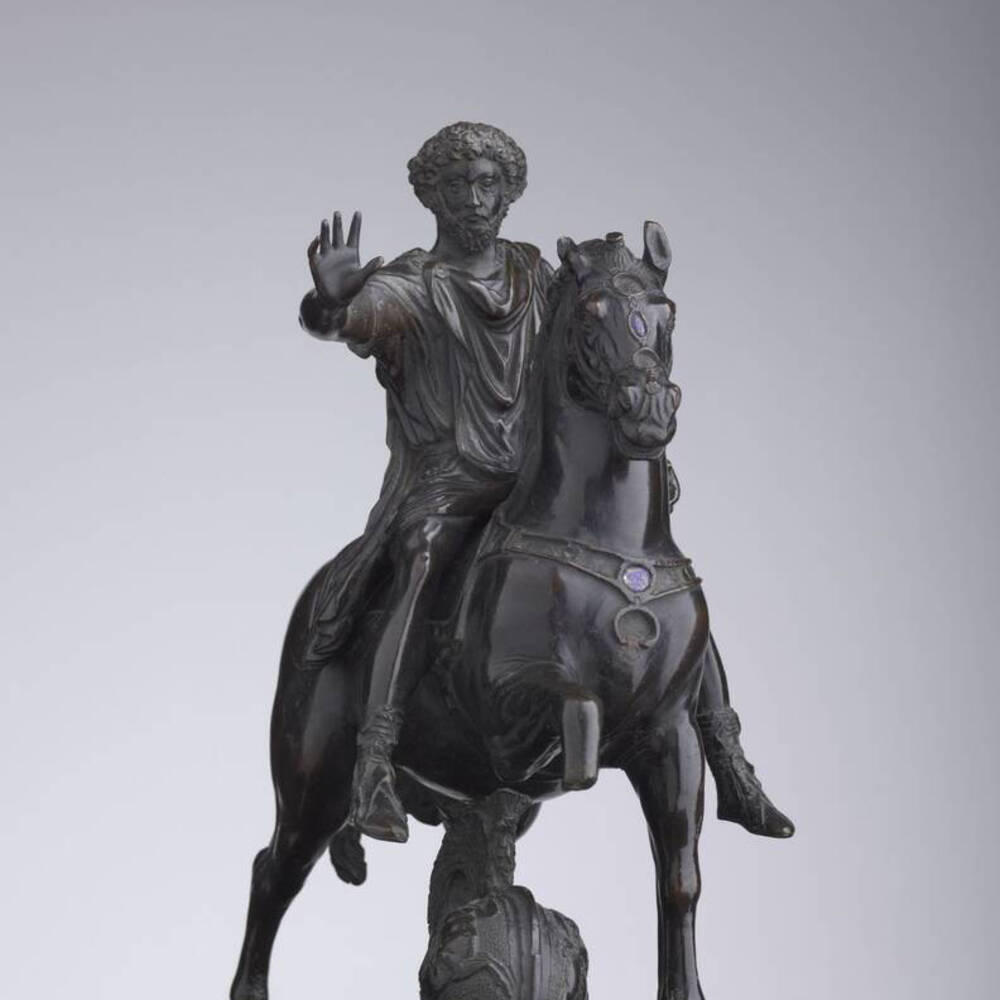
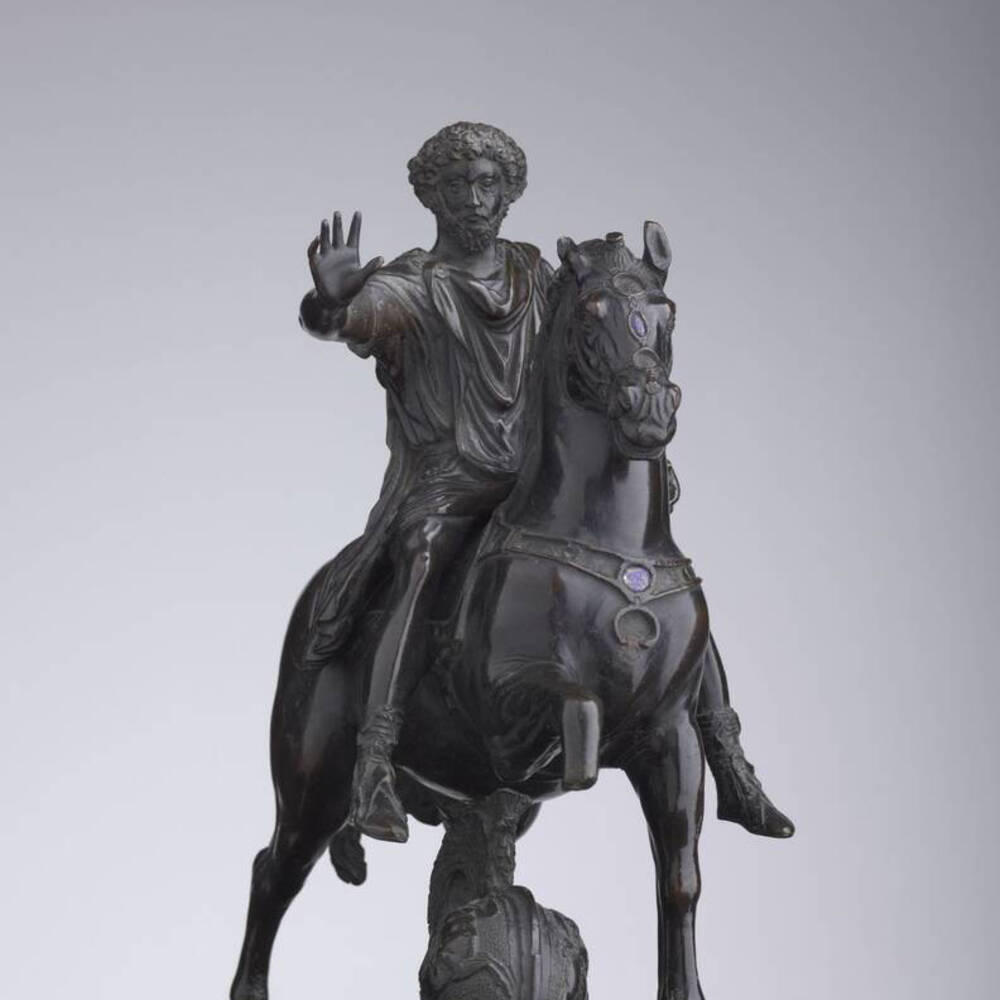
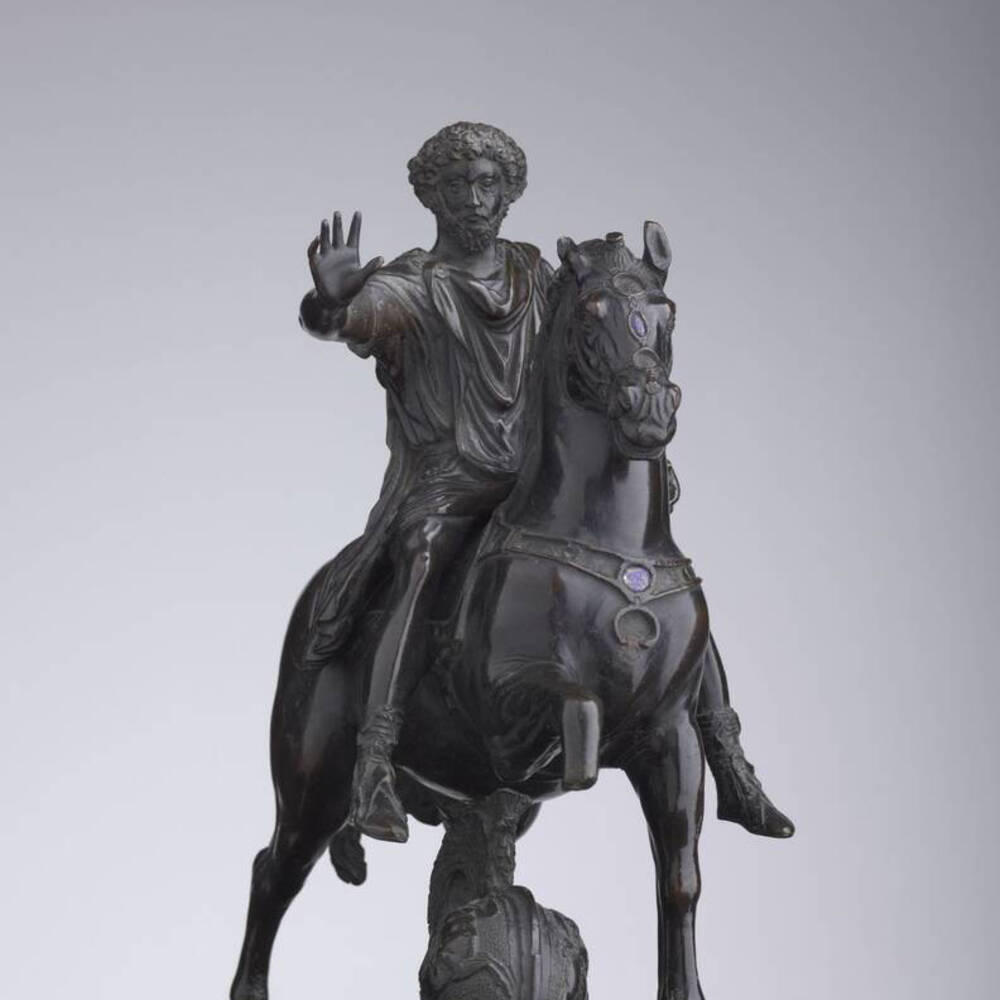
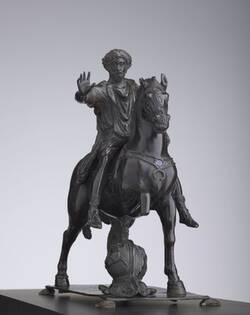
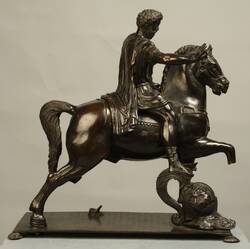
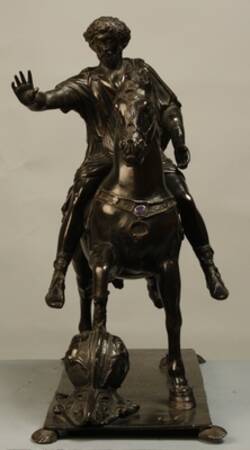
When Filarete first saw the ancient equestrian statue in Rome in 1440, there were different views on which Emperor it depicted. In the Middle Ages, people generally believed it was Constantine the Great – who raised Christianity to the state religion in the Roman Empire. For that reason alone, this statue escaped being melted down, the fate of many other ancient bronzes. Instead, it was preserved as a memorial in front of the Papal Lateran Palace.
Then in the Renaissance, with the growing interest in antiquity, people realised the rider was not Constantine, but were still not entirely sure which Emperor it was. Filarete believed the rider was Emperor Commodus, the son of Marcus Aurelius. But the rider’s real identity as Marcus Aurelius was only discovered in 1538, when Pope Paul III had the statute moved to the new square designed by Michelangelo on the Capitoline Hill. For centuries, the equestrian statue formed the centre of the square. In 1997, the original was replaced by a bronze copy. Today, the valuable original is on view in the Capitoline Museum.
In Filarete’s days, the original equestrian statue was not in particularly good condition. As a specialist for bronze casting, he may well have hoped to receive a prestigious commission to restore it. So his statuette was most likely a working model to show the Pope, as the patron, how he planned to stabilize the statue – by placing a magnificent helmet under the horse’s raised front right leg. In addition, he planned to decorate the bridle with an inlay of coloured enamel. You can still find remnants of the enamel on the bronze statuette.
In fact, the commission to restore the original equestrian statue went to another artist – and so Filarete kept his model. According to the inscription on the base, Filarete later intended to give the statuette to Piero de’ Medici in Florence. But we know of no surviving records to corroborate that. We know this exquisite statuette was in Mantua for a time, until the Duke there presented it to the Saxon court in 1586. By then, small bronze statuettes were already a collector’s item essential in every noble art collection worth the name.
The technique of bronze casting is over 2000 years old. The process, which is quite complex, begins with the artist modelling a figure from wax. The wax figure is then coated with clay and allowed to dry. When the mould is heated, the outer layers of clay are baked and the soft wax inside melts leaving the mould to cast the bronze.
However, given the risk of damage when removing an entire mould, a figure is often not cast as one unit, but in individual pieces. In the next stage, enough molten wax is poured into the moulds to form an even wax layer inside. This needs to be as smooth as possible since it later corresponds exactly to the figure’s ‘bronze skin’. The rest of the hollow mould is then filled with a mix of wet clay and sand. When this core has hardened, the individual pieces covered in wax can be removed from their moulds and joined together to form the entire figure. The pieces are joined with core pins and the wax edges smoothed and joined with a hot knife. At this point, the wax intermodel, as it is called, is fully assembled. In the next stage, wax rods are added to the intermodel to provide channels for the bronze during the casting process.
Then the outer mould is built up. To ensure every detail is reproduced, the clay coating over the figure is added layer for layer. After it has been fired, the massive form is inverted so the melted wax can flow out. As the wax rods, known as sprues, melt and form hollow channels, they provide the route to pour in the hot molten bronze into the mould, and at the same time let the air escape. After the metal cools, the sprues are sawn or chiselled off, the holes filled and, in the last step, the surface cleaned, smoothed and polished.
- Location & Dating
- c. 1440/45
- Material & Technique
- Kupferlegierung (Bronze: Reiter, Pferd, Helm und Messing: Platte und Muscheln), vergoldete blaue Glaseinlagen (SKS, Irene Pamer-Gatzsche, 15.08.2025)
- Dimenions
- H: 38,2 cm, B: 20,0 cm, T: 38,4 cm
- Museum
- Skulpturensammlung
- Inventory number
- H4 155 / 037