In Augustus the Strong’s collection, such monumental sets of Japanese vases were given a prominent place. With their lavish decorations in underglaze cobalt blue, iron red and gold – colour tones characteristic of Japanese imari porcelain – they decorated the Japanese Palace’s entrance hall. Such pieces, exceptionally complex to produce, were made in Japanese porcelain workshops specifically for export to Europe. Their exuberant decorative designs chimed perfectly with the aesthetic taste at royal courts in the baroque period.
Further Media
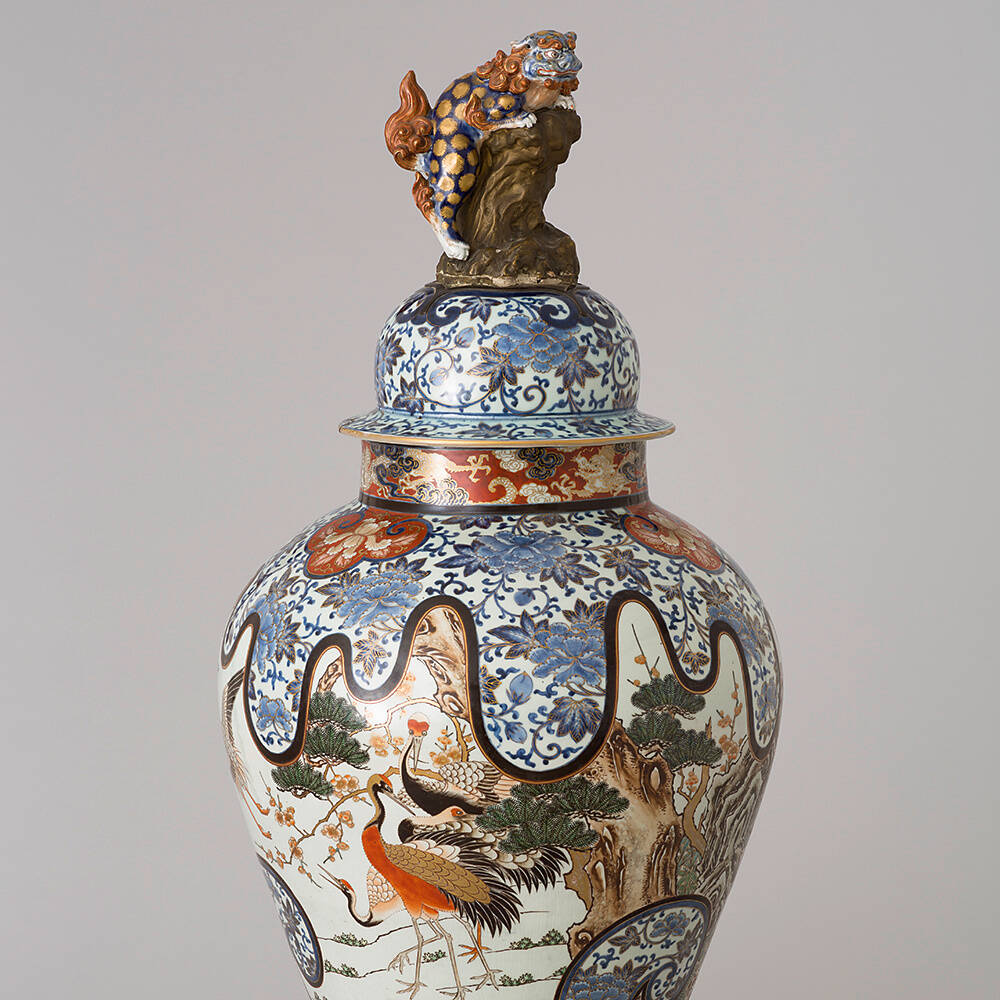
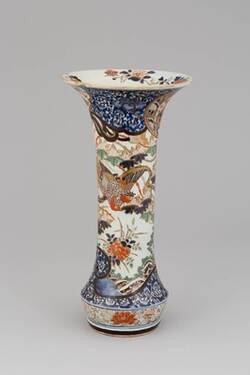
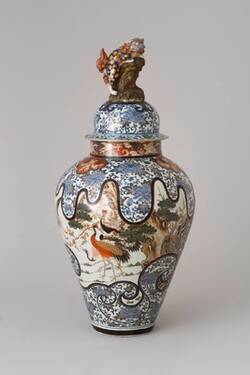
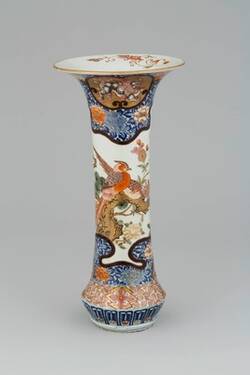
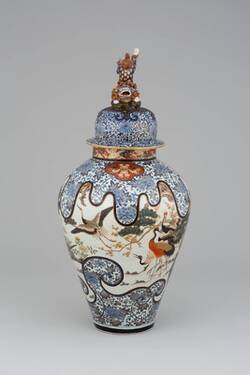
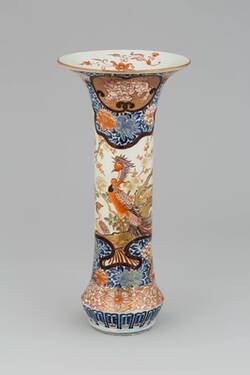
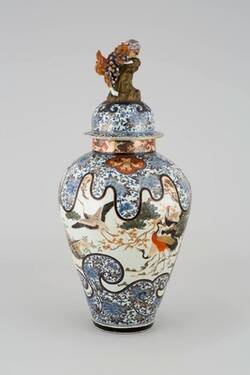
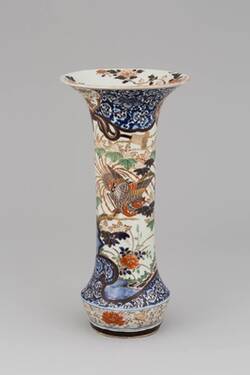
It takes several steps to produce such lavishly painted polychrome pieces. The vases were first shaped on the potter’s wheel and then dried in the sun. Afterwards, the porcelain painter initially added the elements in cobalt blue. This underglaze blue, as it is known, was covered in a transparent ceramic glaze and fired at around 1300 degrees Celsius. Then, the decorative elements in red, black or green were added to the underglaze before the piece was fired for a second time at the relatively low temperature of 800 degrees Celsius. With very few metal oxides, such as cobalt blue, capable of withstanding the high temperatures to fire the glaze, most colours were actually painted onto the glaze after the first firing. In a final step, the gilding was added, and the vase fired a third time at an even lower temperature. Even today, each porcelain maker jealously guards the secrets of the composition of its colours and how they are produced.
- Location & Dating
- Japan, Hizen Province, Arita, Edo period (1603-1868), 1700-1720
- Material & Technique
- Porcelain, painting: underglaze cobalt blue, overglaze colours and gold
- Dimensions
- H. mit Deckel: 90,0 cm, H. ohne Deckel: 59,6 cm, D. 42,0 cm, D. Fuß: 19,2 cm
- Museum
- Porzellansammlung
- Inventory number
- PO 3404